OCTOBOTICS
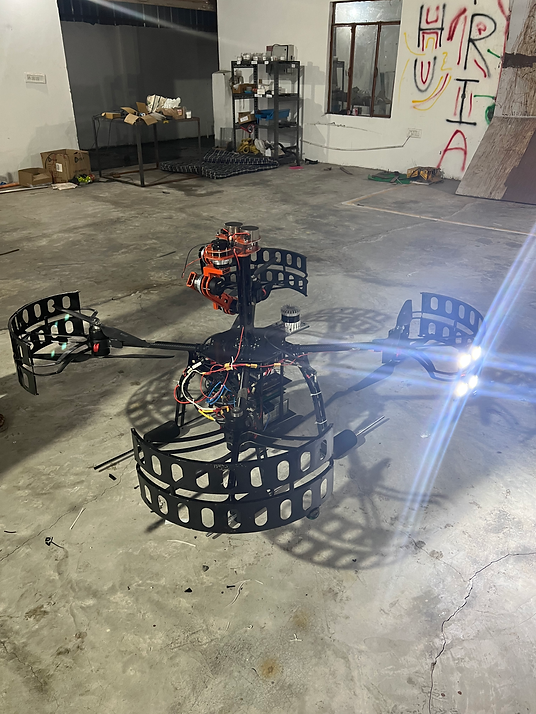
The Project
Octobotics vision is to automate inspection Non Destructive Testing on heavily corroded surfaces for the maritime industry saving human lives in the process
The Prompt
To develop a robot that can achieve Non Destructive Testing of corroded surfaces on the ship (metallic structure)
The Crawler
-
a 3-axis custom tool that has a designed chipping gun a standard Ultrasonic thickness gauge and a grinding tool (Surface Preparation)
-
A 5 DOF manipulator-designed arm that enabled the chipping, grinding, and NDT inspection
-
Worm gear steering mechanism controlled by a DC motor. The crawler has 2 steering motors that allow it to rotate in its position
-
In-house designed N 42 neodymium magnetic wheel
-
Chassis designed for holding batteries and electronics
-
Two versions of the same robot were built A waterproof version that consisted of watertight rotating seals at all the motors and electronics box for underwater operations


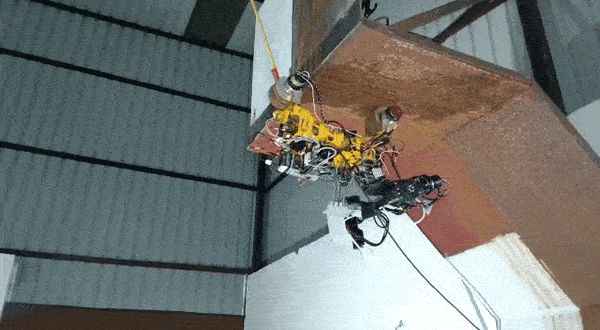
The Inspection Drone
-
To develop a drone that can achieve the NDT services for Horizontal surfaces from down under.
-
The Drone was designed to reach Horizontal surfaces from below.
-
Electro-magnets for latching onto the Horizontal surface.
-
3-DOF RRR manipulator arm for NDT services.
-
Structural members for the drone and bump protectors.
-
Custom Chassis and electronics enclosure.
-
5.8 propellers with a total flight time of 40 minutes.
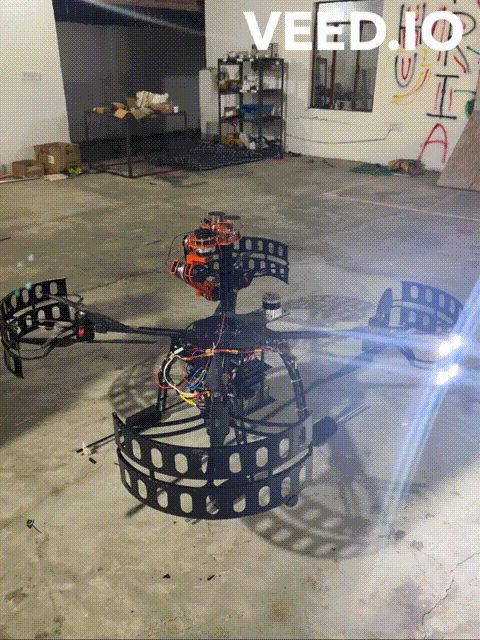
Problems solved
-
The crawling was accurate but prone to falling on rusty, oiled, surfaces where traction is not proper. This meant it would require a tether at all times. I Designed an auto-tensioning device that would maintain tension at all times on the crawler and lock it as soon as it starts to fall.
-
Wrote the Forward and Inverse kinematics for the 5 DOF Crawler arm using DH parameters
-
Wrote the Forward and Inverse kinematics for the 3 DOF Drone arm using DH parameters
-
One of the Major workloads was the Certifications, Standards for robot Design, Rules, and Regulations applied by the industry. As the Shipping industry is heavily regulated. this meant a comprehensive list of standards had to be followed in the processes which are listed below.
-
ABS THE USE OF REMOTE INSPECTION TECHNOLOGIES FEBRUARY 2019
-
ABS SAFETY CULTURE AND LEADING INDICATORS OF SAFETY
-
ABS JOB SAFETY ANALYSIS FOR THE MARINE AND OFFSHORE INDUSTRIES
-
ABS Management of Change for the Marine and Offshore Industries
-
ABS Nondestructive Inspection September 2020
-
ABS RISK ASSESSMENT APPLICATIONS FOR THE MARINE AND OFFSHORE INDUSTRIES MAY 2020
-
ABS SURVEY AFTER CONSTRUCTION 2007
-
ABS PART 7 CHAPTER 1 Conditions for Survey After Construction
-
ABS PART 7 CHAPTER 3 Hull Surveys
-
ABS PART 7 CHAPTER 4 DRYDOCKING
-
ABS PART 7 APPENDIX Guide for Hull Thickness Measurement
-
URZ 10.2 Hull Surveys of Bulk Carriers
-
URZ 7 Hull Classification Surveys
-
URZ 7.1 Hull Surveys for General Dry Cargo Ships
-
URZ 17 Procedural Requirements for Service Suppliers
-
URZ 10.1 Hull Surveys of Oil Tankers
-
URZ 10.3 Hull Surveys of Chemical Tankers
-
URZ 10.4 Hull Surveys of Double Hull Oil Tankers
-
URZ 10.5 HULL SURVEYS OF DOUBLE-SKIN BULK CARRIERS
-
No.76 IACS Guidelines for Surveys, Assessment, and Repair of Hull Structure – Bulk Carriers
-
No. 84 IACS Guidelines for Surveys, Assessment, and Repair of Hull Structures
-
No. 96 IACS Double Hull Oil Tankers - Guidelines for Surveys, (Apr 2007) Assessment and Repair of Hull Structures
-
ROBotics technology for INspection of Ships(ROBINS) Applicable rules and recommendations for the risk management
.
.
and a few more.
-
-
All of these documents had extensive rules and regulations from the shipping classes and were required to be followed for every aspect of the company structure including but not limited to the Design, Fabrication, Manufacturing, and Operations.
-
I led the initiative of consolidating all the rules and requirements for the robot and the company regarding safety refined from all the documents and executing all the changes at the company level leading to the attainment of shipping class certification of the company